For this project, I chose to reverse engineer a conventional brake caliper that we initially purchased off the shelf. My goal was to improve its performance efficiency and enhance its ventilation. The inspiration came from a video I saw about Bugatti's development of their brake caliper, which motivated me to dive deeper into this area. Since I was already working on the FSAE project, I saw a perfect opportunity to apply these concepts and improve our design by using Generative Design.
In this image, from left to right:
1. Original Brake Caliper (Wilwood): The standard caliper that was reverse-engineered and used as the baseline for comparison.
2. Prototype (PLA): A 3D-printed prototype made of PLA material, which was used to test the fit, form, and functionality of the new design before moving to metal fabrication.
3. Prototype (Aluminum and Titanium Alloy): The final prototype made from a combination of AlSi10Mg aluminum alloy and Ti-6Al-4V (Titanium Grade 5), which are both commonly used for lightweight and high-strength components in the automotive and aerospace industries. This version was fabricated for performance testing and further validation of the improved design.
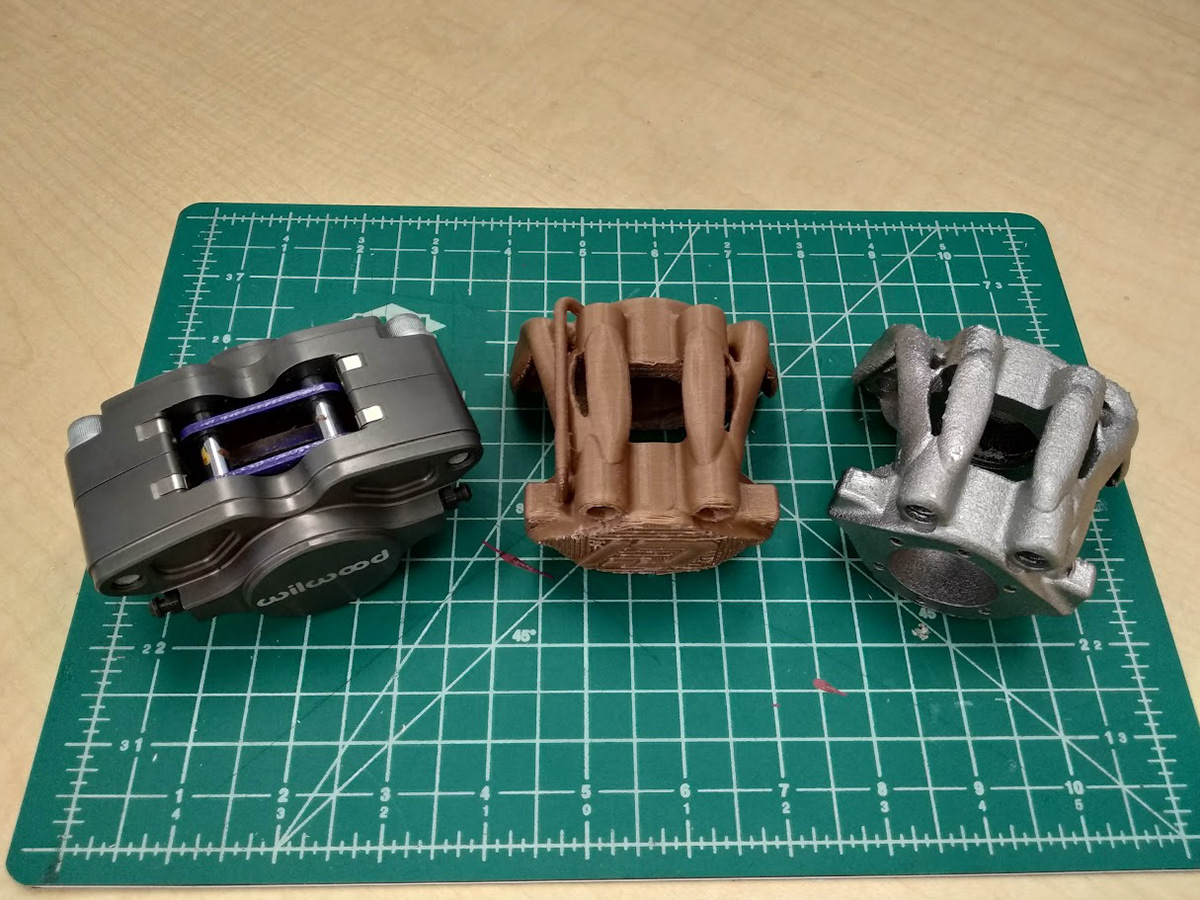
The first image shows the generative design workspace, where the green sections represent the preserved geometry, and the red areas are the obstacle geometry. The blue arrows indicate the load forces being applied to the caliper. This setup allows the software to work around the preserved areas while respecting the constraints provided by the obstacle geometry.
The top-right image highlights the stress reference, indicating how the applied load will affect the caliper. The blue and green areas demonstrate that the caliper can handle the applied forces while withstanding fatigue, ensuring the design will hold up under repeated use.
The bottom-left image displays the post-generation stage, where I reviewed multiple iterations of the caliper design. From these iterations, I selected the design that offered the best combination of strength and aesthetics. The chosen design aligns with my requirements for both performance and visual appeal.
In the final two images at the bottom, I focused on designing the internal fluid pathways. These channels allow hydraulic fluid to flow through both pistons, ensuring they can open and close effectively during braking. The careful design of these pathways is crucial for the caliper's operational efficiency.
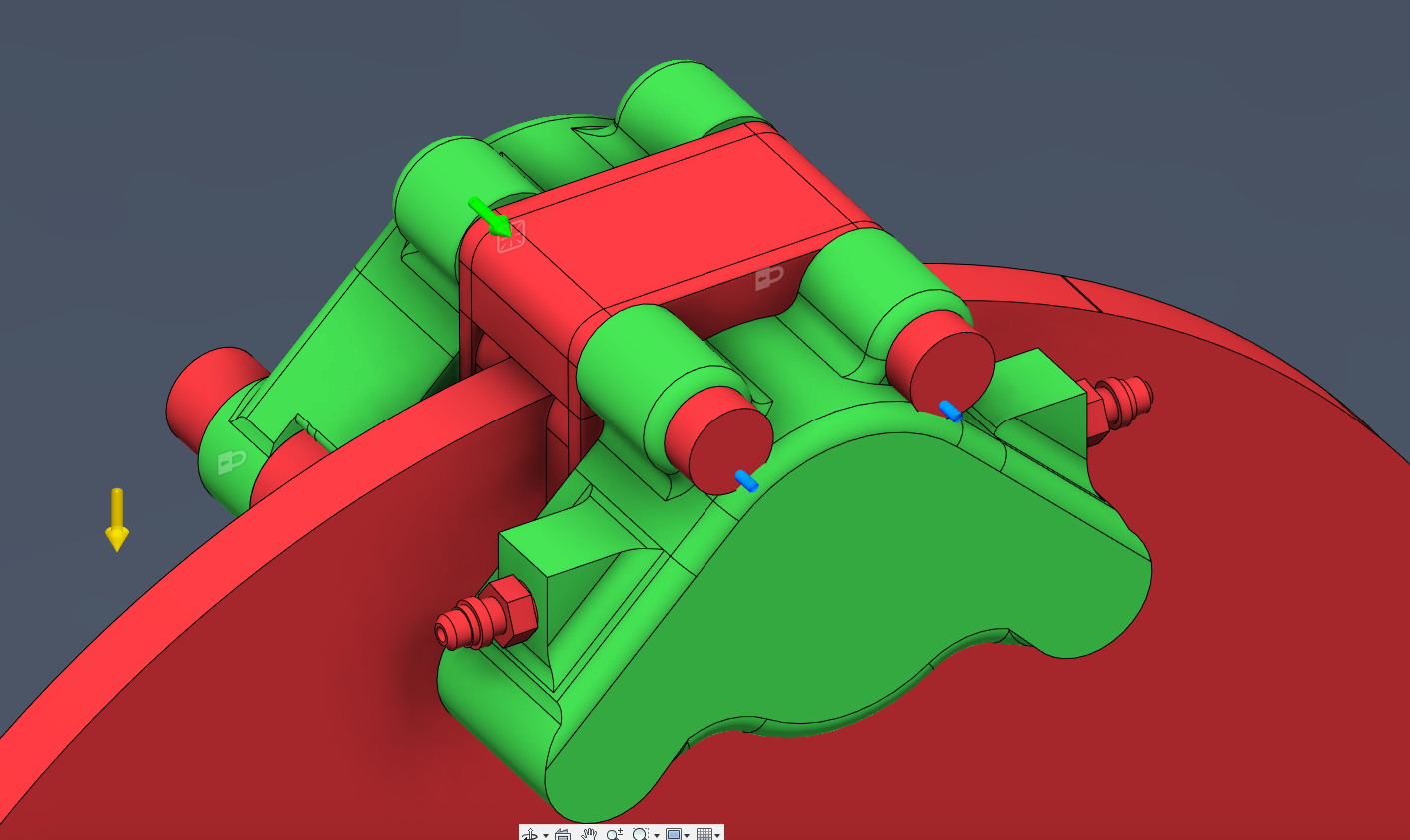
Generative Design - Workspace
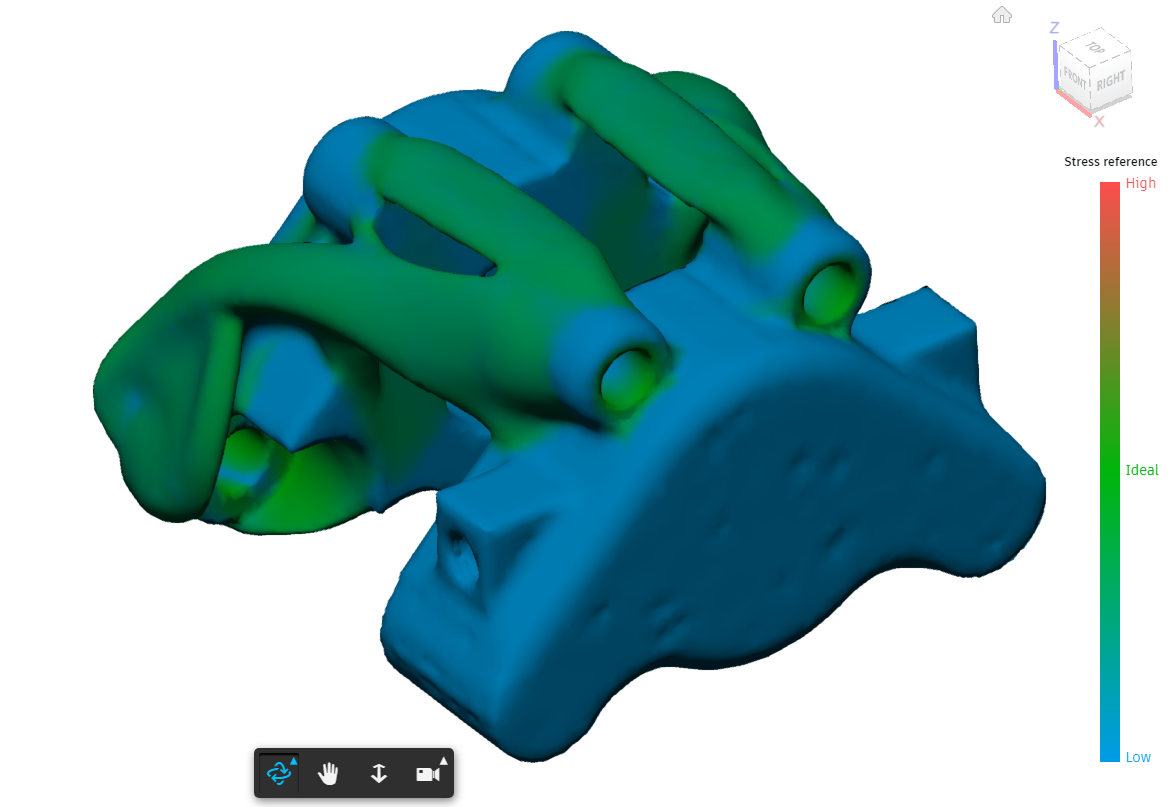
Stress Reference
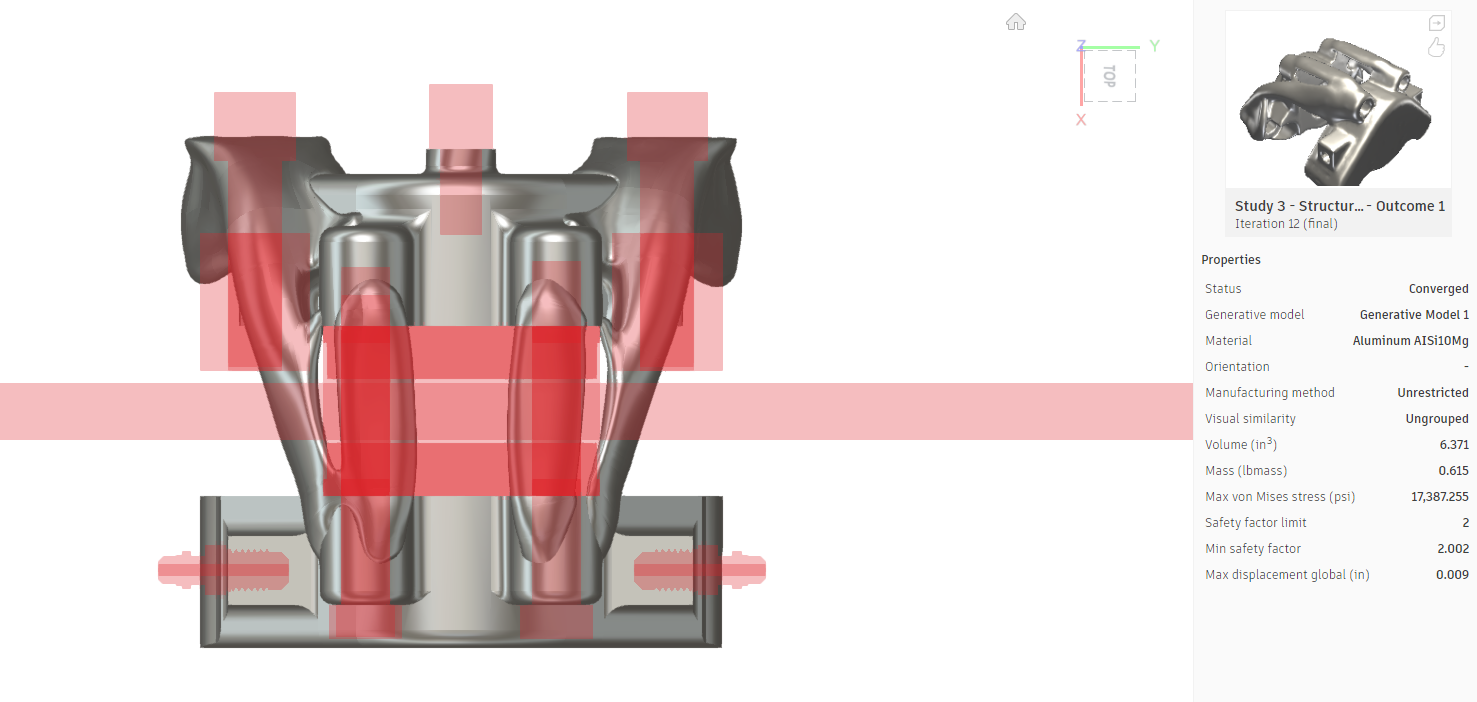
Post Generation
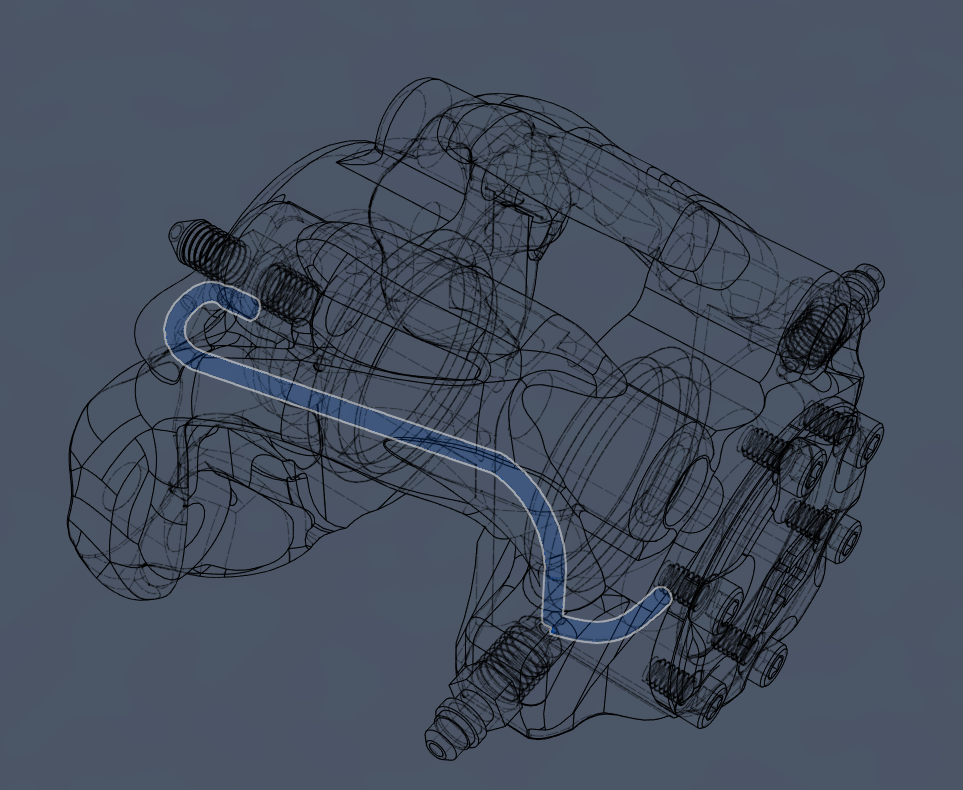
Fluid Line
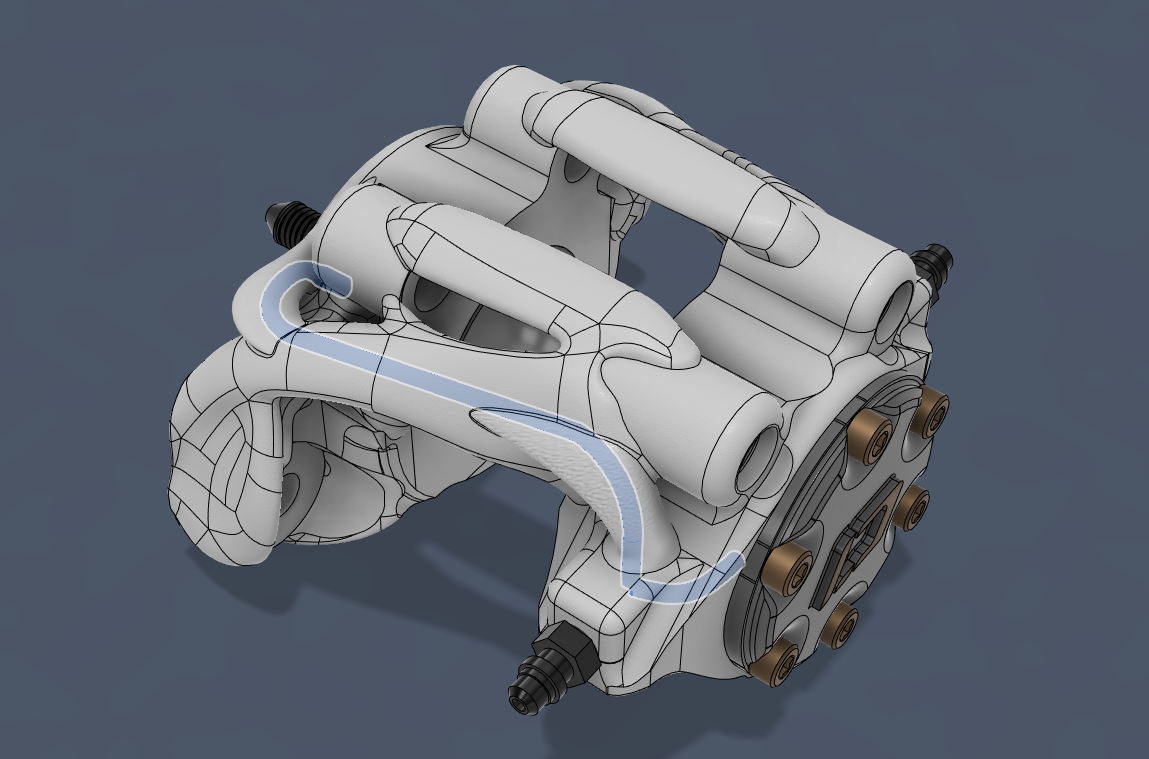
Showcasing the Caliper Assembly
Renderings
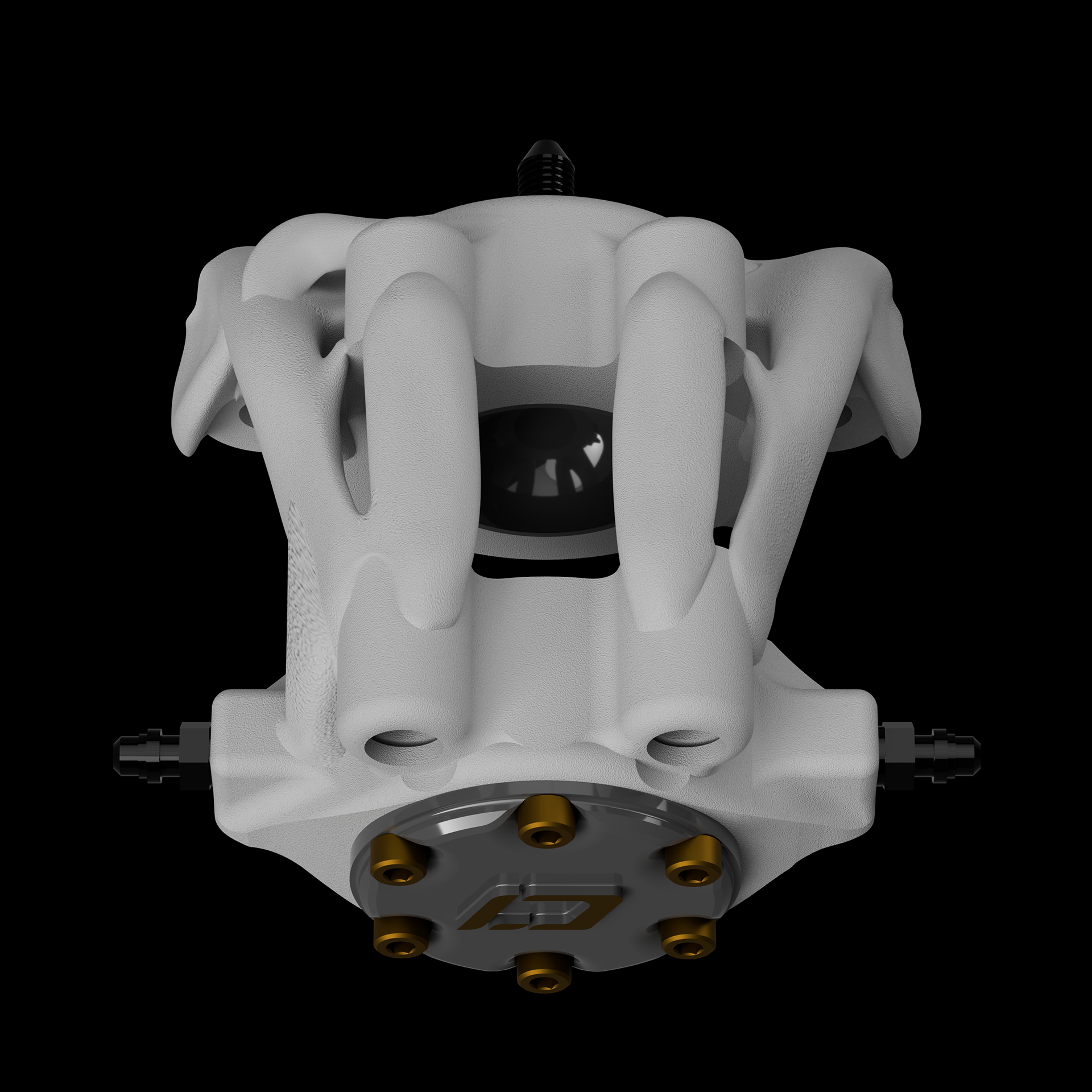
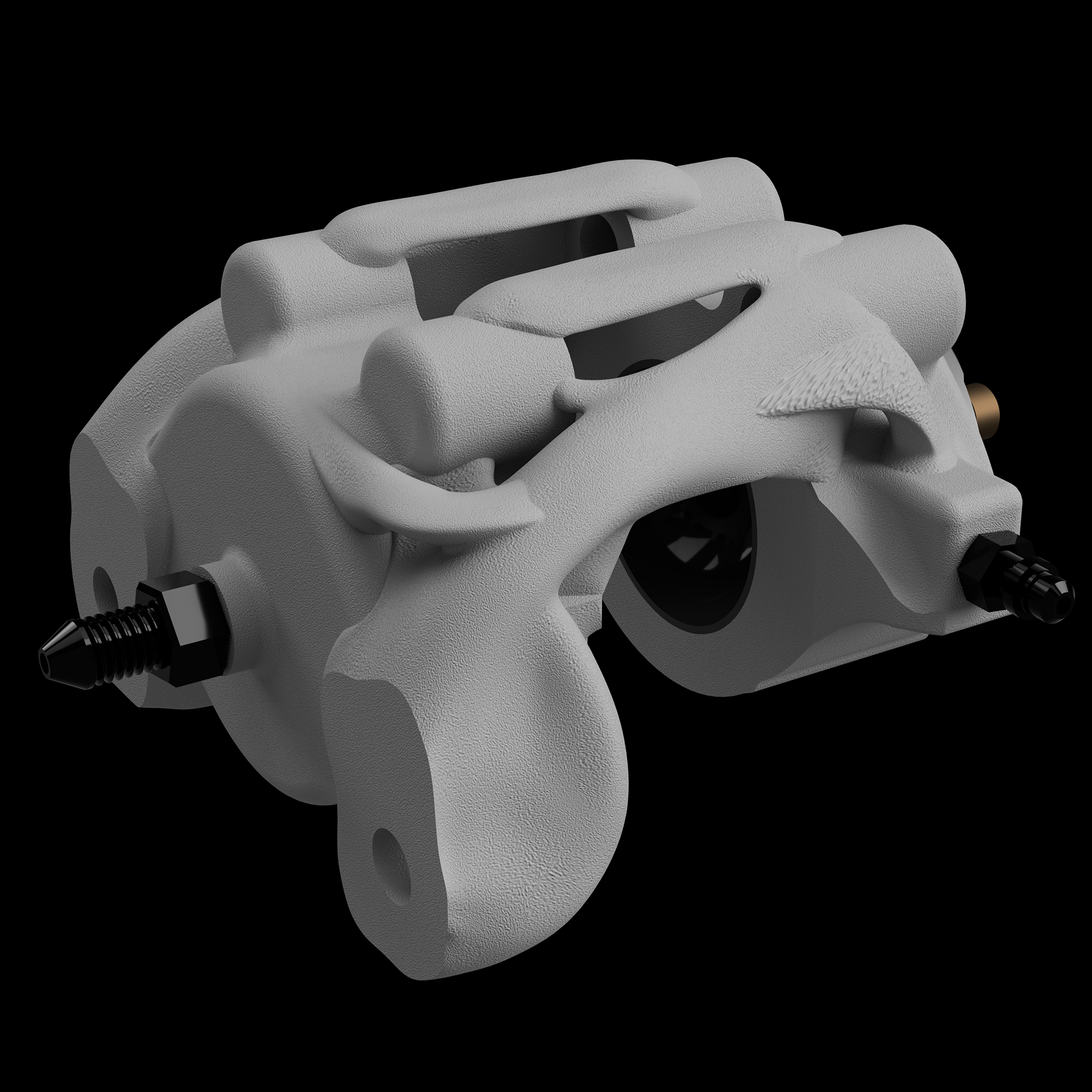
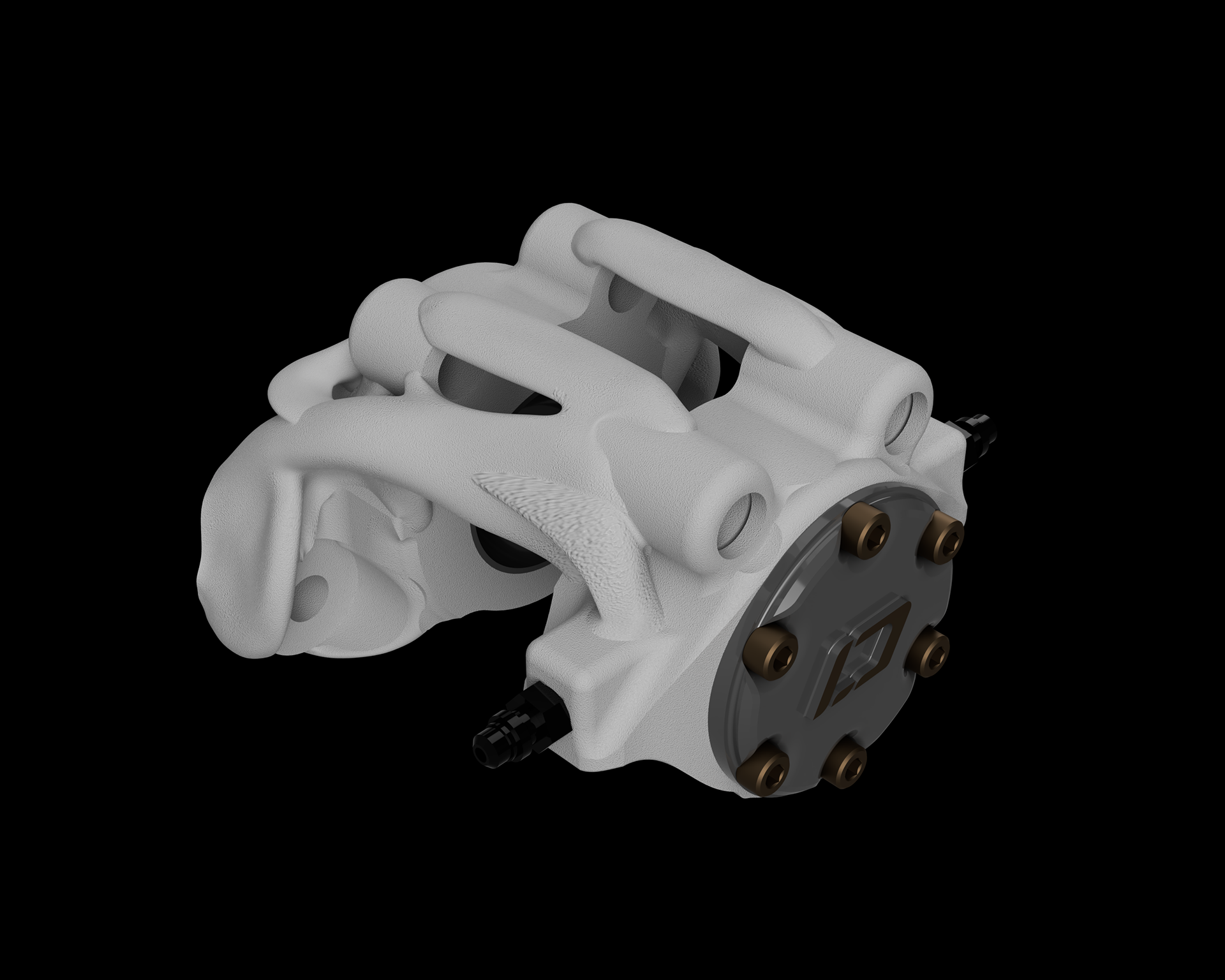
In conclusion, This project showcases the entire journey of reverse engineering a conventional brake caliper and enhancing it through generative design. By using advanced CAD tools and materials like PLA for prototyping and AlSi10Mg aluminum alloy and Ti-6Al-4V titanium alloy for the final prototype, I was able to create a more efficient, lightweight, and performance-driven brake caliper. The new design improves ventilation and performance while maintaining the necessary strength to handle the stress and fatigue experienced during operation. This process not only provided valuable insights into design optimization but also reinforced the importance of iterative testing, material selection, and simulation to achieve high-performance engineering solutions.